Controlling Leakage Across a High Temperature Seal using Differential Pressure
In this application a HORNER APG XL6Â combined touch screen and PLC unit drives a pair of fans extracting gas from large vessels within a vertical chamber furnace.
Â
The vessels are heated to above 500°C during the process, and a connection is needed in the base of the furnace that allows a vessel to be engaged and disengaged from the gas extraction pipe.
Â
A multi-element seal with flexible rings of glass cloth stuffed with ceramic fibre is fitted to a fixed spigot in the base of the furnace. Each vessel is fitted with a matching socket.
Â
The seal is robust and stands the temperature together with repeated engagement  and disengagement, but the environment means a fully tight seal cannot conveniently be engineered.
Â
Seal performance is therefore enhanced by active control of the differential pressure across it.
Â
The 2 m high vessel hangs from the top and expands downwards more than 20mm during the heating cycle.

Differential pressure between the inside of the vessel and the furnace in which it is suspended is continuously monitored and a fan connected to the gas extraction pipe is speed controlled to maintain a small differential pressure of around 5 pascals across the seal. This prevents leakage outward, replacing it with a small and acceptable leakage inward.
Â
The XL6 controls two fans using two PID loops. Smoothing filters are programmed in the controller software and the screen provides a graphical representation of the system with convenient monitoring and adjustment of the working parameters.
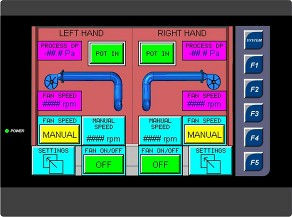

